In the world of pharmaceutical packaging, blister foil thickness plays a pivotal role in ensuring product protection, quality, and longevity. As the demand for efficient packaging solutions in the pharmaceuticals and healthcare sectors continues to rise, understanding the intricacies and importance of blister foil thickness becomes paramount.
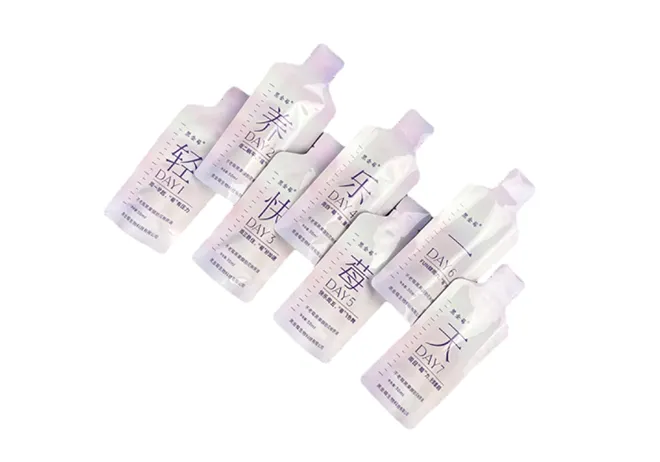
Blister packaging primarily involves a pre-formed plastic, typically PVC, and an aluminum foil as the lidding material. The thickness of the blister foil can significantly impact the package's ability to withstand external pressures, maintain integrity, and provide the necessary barrier against environmental factors.
In recent years, the push towards more sustainable packaging solutions has forced manufacturers to reconsider not just the materials used, but also the thickness of the foils. The trend is leaning towards reducing material usage without sacrificing performance, driving innovation in material technology and manufacturing processes. For instance, while traditional blister foils might range from 20 to 30 micrometers, modern advancements have enabled the creation of thinner foils that still offer robust protection.
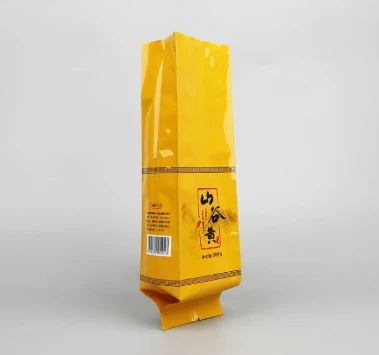
The importance of blister foil thickness extends to protecting the contents from contamination and degradation. Pharmaceuticals, being highly sensitive to moisture, light, and air, require packaging that can provide an effective barrier. Insufficient thickness can lead to permeation, affecting the stability and efficacy of the product within. Thus, for highly sensitive drugs, opting for a thicker blister foil might be advantageous, despite the slight increase in production costs.
Moreover, the aspect of tamper resistance is often a primary concern for manufacturers. A certain thickness level in blister foils can enhance the protective features against tampering, thus ensuring security and maintaining consumer trust. The right balance in foil thickness contributes to an impenetrable seal, deterring counterfeit activities which are prevalently increasing in the pharmaceutical industry.
From a manufacturing perspective, the choice of blister foil thickness can influence the efficiency of the production line. Thicker foils typically provide better machinability and reduce the likelihood of tearing during the sealing and forming processes. However, they may also require more energy during production, which manufacturers must account for when considering cost implications and sustainability goals.
blister foil thickness
On the consumer end,
the tactile experience of using a blister package can be affected by foil thickness. A package that is too stiff or difficult to open might frustrate users, particularly the elderly or those with dexterity issues. Hence, achieving the ideal balance in foil thickness is not only about maintaining product integrity but also ensuring user-friendly accessibility.
Global regulations also dictate specific standards for blister foil thickness in pharmaceutical packaging, ensuring safety and efficacy. Compliance with these regulations is not only a legal obligation but a testament to a company’s commitment to quality and consumer safety. Consequently, companies often conduct rigorous testing and validation processes to determine the optimal thickness for their particular needs.
Emerging trends in the industry, such as the integration of smart packaging solutions, are also beginning to influence considerations around foil thickness. For example, incorporating features such as NFC tags or QR codes might necessitate adjustments in traditional packaging formats and materials, including blister foil thickness.
The competitive landscape propels innovation not only in terms of material usage but also in the development of multi-functional packaging solutions that leverage blister foil's thickness as a key differentiator. Manufacturers that succeed in achieving this balance while maintaining cost-effectiveness and adhering to regulatory standards will undoubtedly secure a competitive advantage.
In conclusion, blister foil thickness is a multi-faceted topic with implications for product safety, manufacturing efficiency, consumer accessibility, and regulatory compliance. As the pharmaceutical and healthcare packaging industries evolve, so too must the approaches to determining the appropriate foil thickness. Through leveraging advanced material technologies and innovative manufacturing processes, companies can enhance their product offerings and build robust, trustworthy packaging solutions that meet the evolving demands of modern consumers.