Pharmaceutical aluminum foil stands as a cornerstone in modern medicinal packaging, playing a pivotal role in the storage and delivery of drug products. This material is not merely a packaging element; it epitomizes a blend of science and precision, specifically designed to meet stringent pharmaceutical requirements.
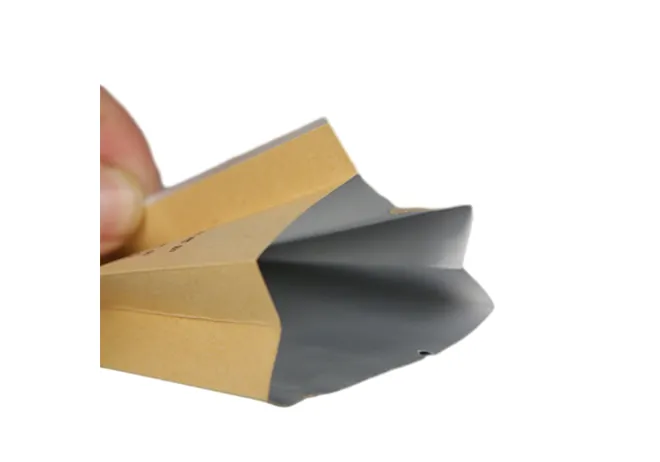
Precision-engineered, pharmaceutical aluminum foil provides exceptional barrier properties against moisture, oxygen, and light – all of which can potentially degrade medication. Its impermeability factors ensure that once a product is sealed, external conditions cannot influence the medication's efficacy or shelf life. This makes aluminum foil a preferred choice among leading pharmaceutical manufacturers who prioritize product integrity and patient safety.
The expertise invested in producing pharmaceutical-grade aluminum foil ensures it meets the rigorous standards set by regulatory bodies such as the FDA and EMA. Producers employ multi-step processes including rolling, annealing, and surface treatment to achieve the desired thickness and surface finish that adheres precisely to industry specifications. The foil is often laminated or coated with materials that enhance its protective capabilities or enable compatibility with other packaging components such as blister packs.
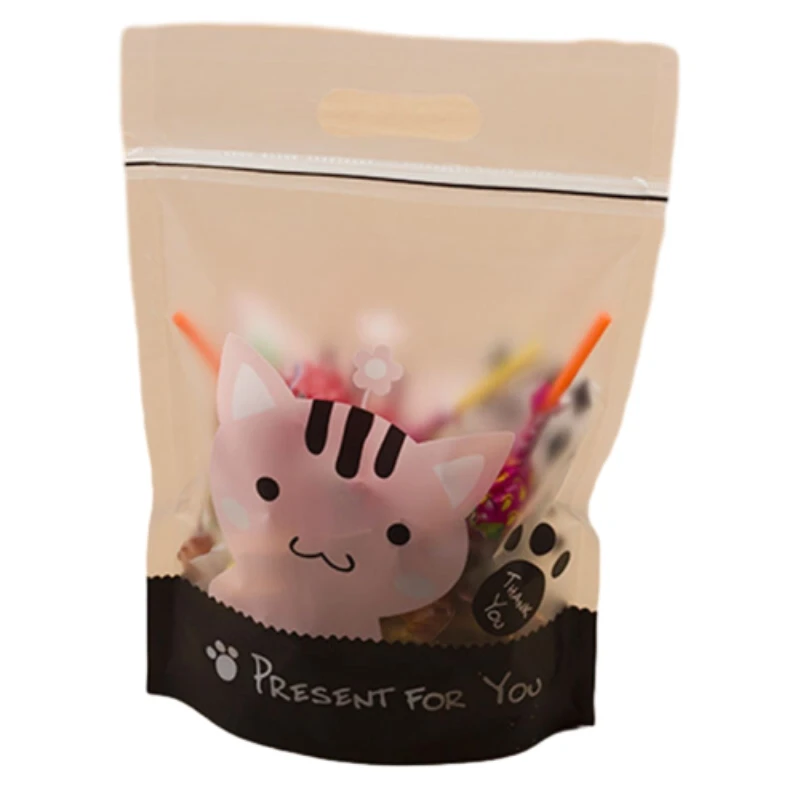
Trust in pharmaceutical aluminum foil is further reinforced through its historical track record of effectiveness. Numerous studies and years of industry application have validated its performance in varied climates and environments, proving its universal applicability. Additionally, case studies highlight successful use in encapsulating a wide range of pharmaceuticals, from tablets to high potency drugs, showcasing its versatility.
One key authoritative advantage of using aluminum foil in medicinal packaging is its sustainability aspect. Unlike many traditional packaging materials, aluminum is infinitely recyclable, offering a greener alternative that aligns with global environmental goals. Companies committed to sustainable practices appreciate this, as it not only reduces waste but also enhances their corporate responsibility profile.
pharmaceutical aluminum foil
In terms of real-world experience, pharmaceutical professionals frequently commend aluminum foil for its ease in forming and sealing, which enhances manufacturing efficiency. Its adaptability means it can be custom-designed to fit myriad product configurations, from simple strips to complex multi-compartmental blister packs. Feedback from packaging specialists often highlights the material’s ability to consistently provide a reliable seal without compromising on speed, a critical factor in high-volume production settings.
Developing trust among end-users—patients and healthcare professionals—is of utmost importance. Patients value medication that maintains its integrity from the manufacturing line to their medicine cabinets. Pharmacists and healthcare providers rely on such dependable packaging to reinforce compliance and aid in accurate dispensing.
Moreover, innovations in surface engineering have advanced the capabilities of pharmaceutical aluminum foil further. For instance, anti-counterfeiting features can be integrated directly into the foil, providing additional security against the infiltration of fake pharmaceuticals into the supply chain.
To sum up, pharmaceutical aluminum foil is more than just a packaging solution. It represents a synthesis of scientific advancement, environmental stewardship, and operational excellence. Its continued evolution and application ensure that it stays at the forefront of pharmaceutical packaging, embodying safety, reliability, and trust that both the industry and consumers rely upon.